Henry Ford didn’t invent the automobile. It’s a common misconception. It was actually Karl Benz who invented the first steam-powered three-wheeled Motor Car known as the Motorwagen, in 1886.
But what Ford did was something even more worthwhile: his company invented the moving assembly line, a method of production that could finally allow manufacturing cars at scale.
Not only did the moving assembly line revolutionize car manufacturing, but it also revolutionized the entire manufacturing industry.
Here’s the full story of how it happened.
Henry Ford built his first car, which he named the Quadricycle, in 1896. In 1903, he founded the Ford Motor company and launched the Model T five years later.
Model T wasn't the first car Ford created. It was his ninth. But it is the one that would go on to achieve mass popularity and become an icon — all thanks to the introduction of the moving assembly line in 1913.
Before 1913, Ford and many other car makers put together entire cars at one station. A team of workers laboured on each car individually. When it launched, the Model T's price was set at $850, which would be approximately $25,000 in today’s currency. That was cheap, but still not cheap enough for the masses. Ford needed to find a way to cut down the price even further.
As a result, till 1913, the Ford Motor Company was a decade-old company with large ambitions, but it had hardly transformed American life. Henry Ford had a goal of making automobiles for the multitudes. The Model T was his answer to that dream; he wanted them to be both sturdy and cheap. But its manufacturing process was inefficient and hardly complemented the company's lofty goal of producing two hundred engines per day. Workers still had to fetch parts from multiple bins and move them around on hand trucks.
All of this changed in 1913.
One day, one of Ford's employees — Bill Klann — was at a Chicago slaughterhouse. There, he saw how the slaughterhouse had achieved industrial levels of efficiency: animal carcasses moved by on overhead trolleys, while a series of butchers performed specialized tasks in sequence as the carcasses advanced.
As Klann watched this, he had an idea: dismantling a carcass was fundamentally similar to building an engine; therefore, adopting a moving assembly line at Ford would increase productivity and reduce costs.
“If they can kill pigs and cows that way, we can build cars that way,” Klann told his boss upon his return. His boss couldn't see how dismantling flesh and assembling machinery could be related.
Klann insisted that it was the same thing.
Eventually, the idea reached Henry Ford, who saw that the most crucial feature of this assembly line was the conveyer belt. Moving the product to the worker seemed like a better use of time and resources. Consequently, The Ford Motor Company team decided to try to implement the moving assembly line in the automobile manufacturing process.
After much trial and error, on December 1, 1913, Henry Ford and his employees successfully introduced the moving assembly line at the Highland Park assembly plant.
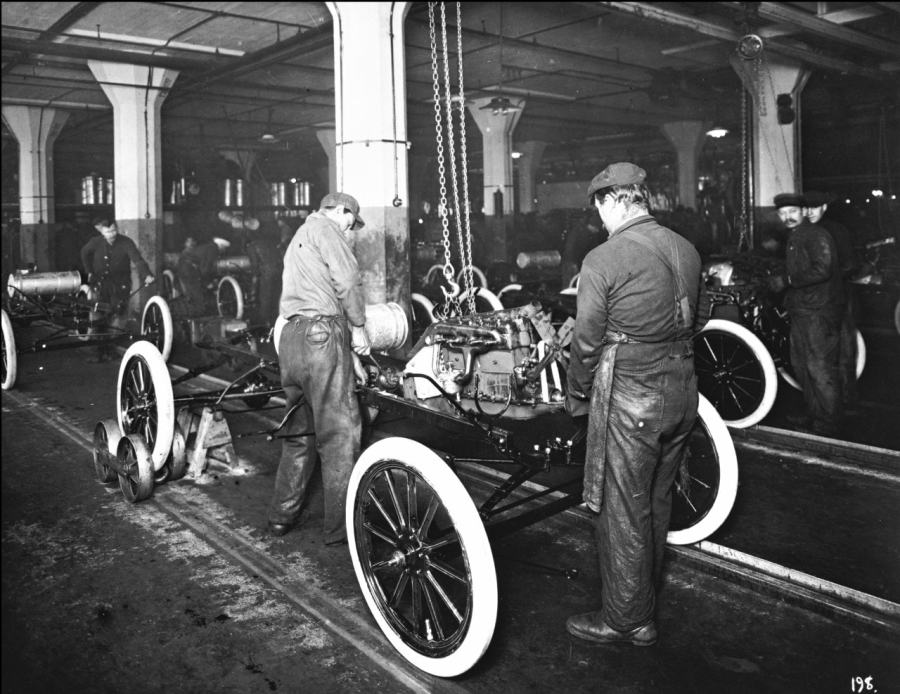
Henry Ford famously remarked that the use of the moving assembly line allowed for the work to be taken to workers rather than the worker moving to and around the vehicle. The vehicle began to be pulled down the line and built step-by-step. At first, it was pulled by a rope, and later it became a simple moving chain mechanism.
In total, the manufacturing of the car was broken down into 84 steps. Parts were created in mass quantities and then brought directly to the workers who were trained to work at that specific assembly station. The chassis of the car was pulled down the 150-foot line by a chain conveyor and then 140 workers applied their assigned parts to the chassis. Other workers brought additional parts to the assemblers to keep them stocked; this reduced the amount of time workers spent away from their stations to retrieve parts.
As time passed, Ford used multiple parallel lines in a start-stop mode to adjust output to large demand fluctuations, along with many other macro- and micro-optimisations across the supply chain.
The impact of the moving assembly line was revolutionary.
The new process made it so that the Model T was now built in only 90 minutes instead of the original 12 hours. In 1914 alone, the Ford Motor Company produced 308,162 cars: a number that exceeded the number of cars produced by all other automobile manufacturers combined.
With this, Ford was simultaneously able to increase his profit margin while lowering the cost of the vehicle to consumers. He was eventually able to drop the price of the car from $850 to $260 in 1924.
However, in terms of immediate impact, in 1913 alone, Ford had to hire more than 52,000 workers for a workforce that at any one time numbered 14,000. He increased the company’s wage rate to $5 per 8-hour workday, while the norm for that time was about $2.25 for a 9-hour workday — a more than 2x jump in wages for employees while having to work an hour less, not more, every day!
And all of this was possible due to a simple analogical insight by one of his employees.
Klann could see beyond the superficial differences between slaughtering animals and assembling cars. There, at the heart of both processes, he saw an underlying structural analogy waiting to be exploited.
Seeing Ford’s success, it took little time for almost every other manufacturing industry to implement the moving assembly line, creating a tonne of wealth and growth for businesses and society at large.
Sources:
Henry Ford and the Auto Assembly Line
How Steve Jobs’s Mastery Of Analogies Sent Apple Skyrocketing
In 1913, Henry Ford Introduced the Assembly Line: His Workers Hated It